Simplifying hospital linen management with RFID inventory solutions
Discover how a linen tagging system can transform a hospital’s laundry operations with smart tracking technology.
Simplifying hospital linen management with RFID inventory solutions
Discover how a linen tagging system can transform a hospital’s laundry operations with smart tracking technology.
If your laundry business is still tracking towels and scrubs with clipboards or spreadsheets, you’re not just behind—you’re bleeding money.
Let’s consider a few examples: A hospital needs 500 sterile gowns STAT, but your team can’t find them. A luxury hotel cancels its contract because sheets keep vanishing. A factory delays production because uniforms are stuck in a wash cycle black hole.
These are daily realities for laundries relying on legacy tracking. But what if every linen, uniform, and textile in your facility could tell you exactly where it is, down to the square foot?
That’s the power of RFID inventory solutions.
If your laundry business is still tracking towels and scrubs with clipboards or spreadsheets, you’re not just behind—you’re bleeding money.
Let’s consider a few examples: A hospital needs 500 sterile gowns STAT, but your team can’t find them. A luxury hotel cancels its contract because sheets keep vanishing. A factory delays production because uniforms are stuck in a wash cycle black hole.
These are daily realities for laundries relying on legacy tracking. But what if every linen, uniform, and textile in your facility could tell you exactly where it is, down to the square foot?
That’s the power of RFID inventory solutions.
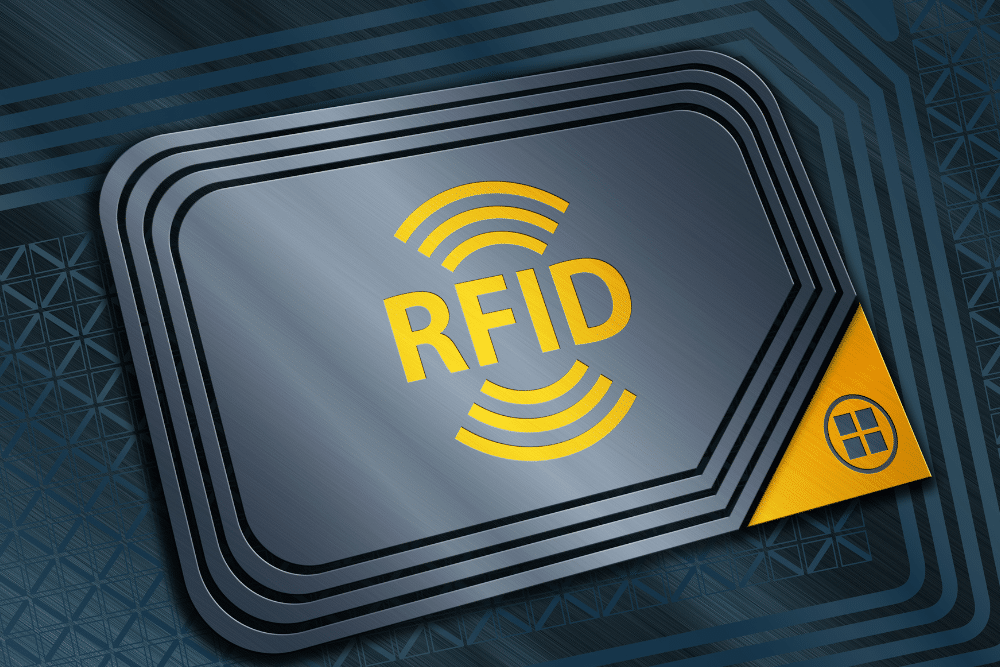
Getting to know RFID technology for laundries
The cost of guessing games
Manual inventory management isn’t just inefficient—it’s a financial sinkhole. Every year, a substantial number of linens vanish due to poor tracking, leading to financial losses. Hospitals risk penalties accounting for thousands of dollars for non-compliance with inventory audits. Manual tracking errors contribute to frequent over-ordering, stock discrepancies, and supply chain disruptions. Additionally, the lack of real-time visibility causes delays in laundry processing and distribution. RFID technology eradicates these issues entirely, ensuring precise tracking, reducing labour costs, and preventing unnecessary waste. This technology transforms inventory management from a chaotic guessing game into an exact science, delivering reliability and efficiency at every stage of the process.
How RFID inventory solutions work
RFID technology enables real-time inventory tracking with minimal manual intervention. RFID tags are embedded into linens, engineered to endure many hundreds of industrial washes without degradation. These tags transmit data to RFID readers, which detect and log each item’s location using wall-mounted sensors or handheld scanners. The technology tracks every item’s journey across wash cycles, storage facilities, and distribution channels. RFID-enabled software automates the logging of all inventory movements, reducing the need for tedious manual record-keeping. Advanced analytics pinpoint inefficiencies, offering actionable insights to optimise stock levels. With RFID, businesses gain unparalleled control over their inventory, eliminating waste, boosting efficiency, and maintaining accuracy.
Why RFID is the ultimate difference maker
With RFID, shrinkage has become a problem of the past as RFID prevents theft and tracks missing linens in real time. Labour costs are significantly reduced, as RFID scanning cuts down an eight-hour manual inventory process to just a few minutes. Automated logs ensure seamless compliance with industry regulations, eliminating the risk of audit penalties. Predictive analytics optimise stock levels, preventing over-ordering and waste while streamlining demand forecasting. Transparent inventory reports build customer trust, offering clients clear insights into linen usage. Workflow efficiency improves across sorting, washing, and delivery, reducing operational bottlenecks. With RFID in place, laundry facilities achieve precision at every step, minimising errors and increasing profitability.
Key features of modern RFID inventory solutions
Not all RFID systems offer the same level of performance, making it crucial to choose a solution with essential features. Industrial-grade RFID tags ensure longevity, resisting bleach and high temperatures. Real-time dashboards provide instant visibility into inventory levels across multiple locations, enabling remote monitoring. Seamless system integration ensures that RFID technology synchronises with existing asset management software without disruptions. Advanced theft prevention mechanisms, such as geofencing, send alerts when linens exit designated areas. Customisable reports allow for detailed, client-specific insights for better inventory tracking. Advanced analytics enhance operational efficiency by identifying trends, predicting supply needs, and reducing stock inconsistencies.
Transform your laundry operations with RFID inventory solutions
Traditional linen tracking methods lead to lost inventory, compliance risks, and rising operational costs. RFID technology eliminates these challenges by providing instant visibility into every item’s location and lifecycle. With automated tracking, seamless system integration, and real-time inventory updates, you can reduce shrinkage, streamline workflows, and ensure audit-ready compliance.
Traditional linen tracking methods lead to lost inventory, compliance risks, and rising operational costs. RFID technology eliminates these challenges by providing instant visibility into every item’s location and lifecycle. With automated tracking, seamless system integration, and real-time inventory updates, you can reduce shrinkage, streamline workflows, and ensure audit-ready compliance.
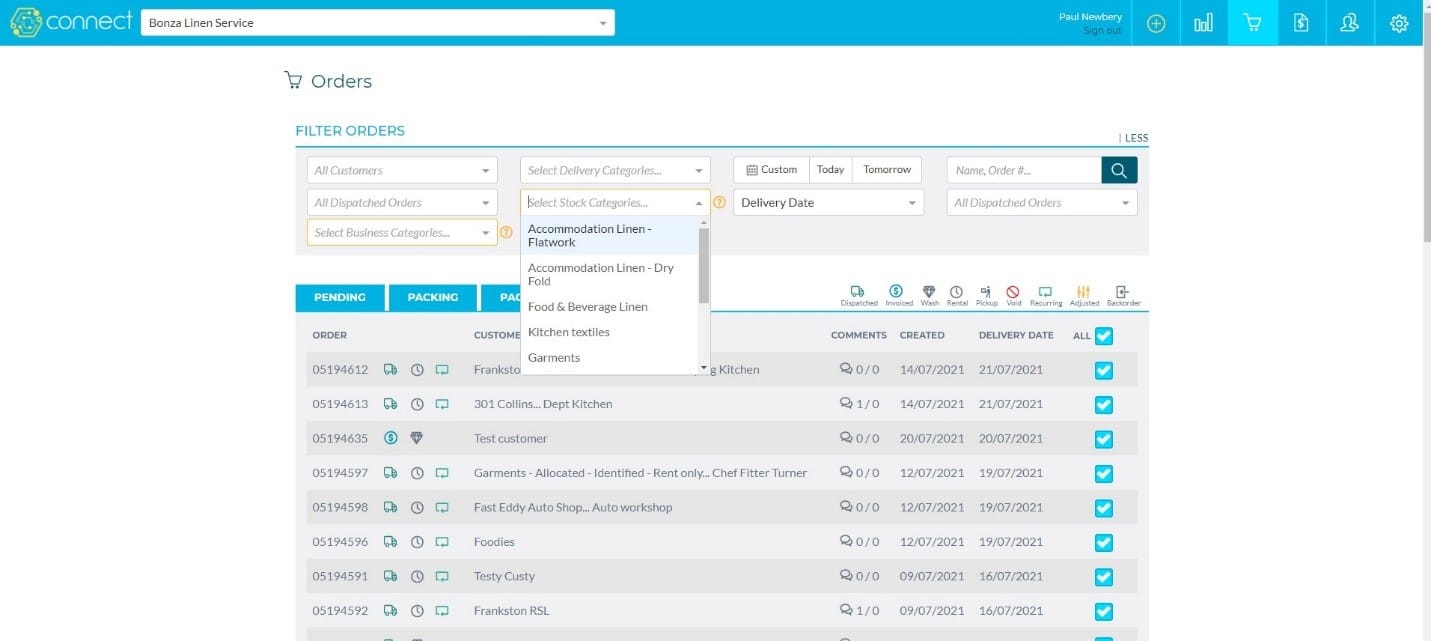
Client success stories
"The transition to Bundle has been instrumental in Allied Laundry continuing to drive change and business improvement by providing real-time customer ordering information, streamlined ordering, and billing processes and have enabled a considerable reduction in staff time. The system has been a real success story for Allied Laundry."
Mark Mabbet
Allied Laundry Service
"No question is a stupid question in the eyes of the Bundle team. Their customer service, expertise and knowledge ensured a smooth transition for me when I purchased my business. The system is user friendly and easy to navigate, while syncing seamlessly with my accounts package."
Geraldine Minogue
Associated Laundry Services
Since the transition from a manual, paper-driven system to Bundle, the time spent managing orders through to invoicing has been reduced by some 75%. From an administrative perspective, it is far easier to track the progress of orders, respond to queries (and resupply dockets).
The management abilities for individual account needs with set days, recurring orders, fixing cut-off times, adding notes to orders and pick-ups means that all relevant persons have the same information.
Customer support is also given a high priority and queries and concerns are met promply and efficiently.
Cynthia Hertrick
Blueline Laundry
Book a demo
Transform how you manage laundry inventory with Bundle. Get in touch with us to book a demo.
FAQs
Yes, RFID technology is built for seamless integration. Modern RFID readers and software platforms are designed to work alongside existing laundry and asset management systems without requiring costly equipment replacements. Whether you use conveyor systems, tunnel washers, or traditional sorting stations, RFID readers can be installed to track items without disrupting workflow. This allows laundries to upgrade their tracking capabilities without overhauling their operations.
RFID solutions prioritise data security through encrypted tags, secure cloud storage, and controlled access protocols. Encrypted RFID chips prevent unauthorised scanning, ensuring only approved systems can access inventory data. Additionally, cloud backups and real-time monitoring help safeguard critical information, reducing the risk of data loss or breaches. With multi-layered security features, businesses can confidently manage inventory without compromising sensitive client information.
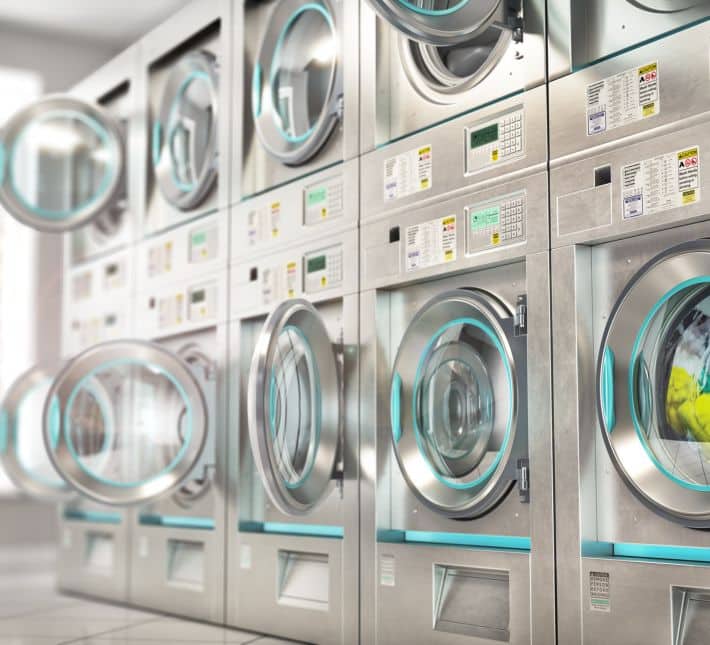